山口県光市にある光工場。グローバルに展開するタケダにおいて最大規模を誇るこの工場に、世界が注目する施設があります。それが固形製剤包装施設。2021年にファシリティー・オブ・ザ・イヤー・アワード(年間優秀施設賞)を受賞した、製薬業界初の技術革新に迫ります。
製薬業界で初めて実現した
自動ラインクリアランスシステム(ALC)
光工場で製造された医薬品のうち、錠剤のものは固形製剤包装施設に運ばれ、包装される。まずは、錠剤をプラスチックとアルミで挟んだPTPシート※1に装填し、それを添付文書※2と共に箱詰めする。
その後、ロット番号や使用期限等を印字して、最終製品をダンボールに詰める。この包装工程全体で人の手が入ることを最小限に抑えられるように、機械により自動化している。
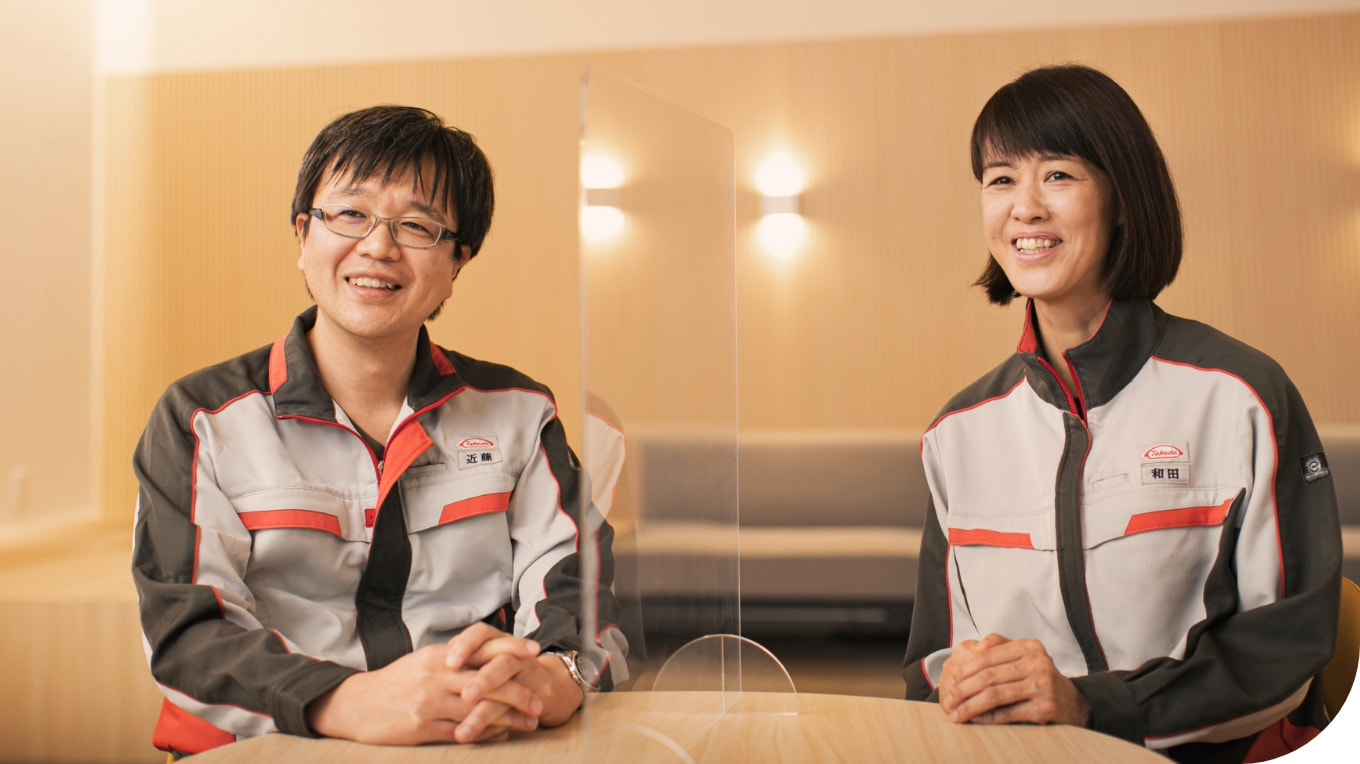
「最終製品を箱詰めしたダンボールを、倉庫に搬送するまでの工程にもロボットを導入し、極力人の手を排除して効率化を図っています」と教えてくれたのは、包装工程を管理するインスペクション&パッケージング部の近藤だ。
光工場の固形製剤包装施設が注目を集めているのは、包装工程の自動化だけではない。人々の健康や生命に直接関わる医薬品を製造するには、定められた品質規格に適合しているのはもちろんのこと、製造工程を適切に管理することが求められる。
そのガイドラインとなっているのが、GMP(Good Manufacturing Practice)」だ。
GMPでは医薬品の異種混入を防ぐため、包装する薬を切り替える際に包装ラインの工程をすべてチェックする、ラインクリアランスの徹底が定められている。
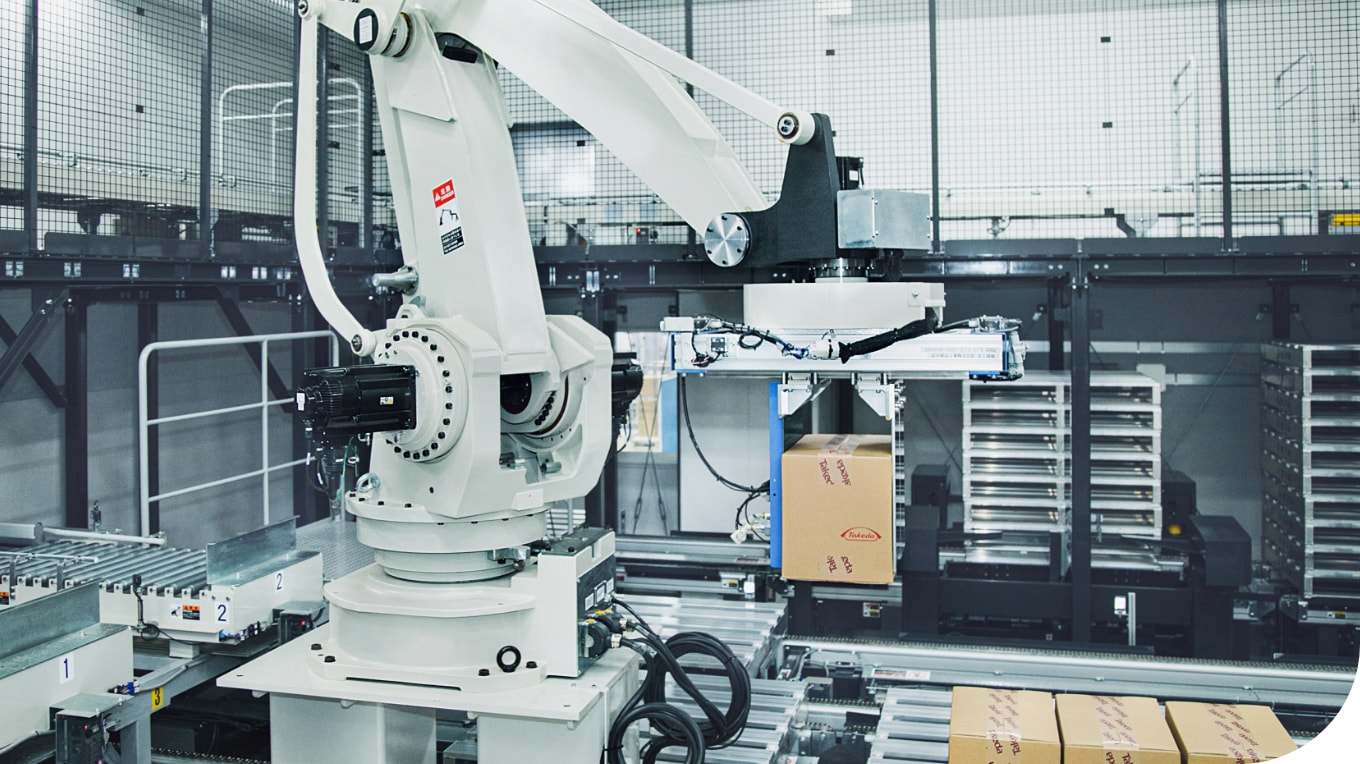
光工場では、この工程を自動で行うALCを製薬業界で初めて導入した。
「これまでは包装ラインの確認作業を、隅々まで人の目で行っていました。安全面にも気を配りながら、機械の下はもちろん、カバーを開けて機械の中までのぞき込んで残留物がないかをくまなくチェックするので、30分はかかっていました」と話すのは、固形製剤包装グループ・マネジャーの和田。
「時間のロスも大きいですが、何よりも人の目だけではどうしても限界があります。そこで、残留物の見逃し検査を安全に、より完璧に実施することを目指して、ラインクリアランスの自動化に踏み切りました」
ALCでの残留物検査には、360°カメラとレーザーセンサー、さらに、それらの設置が困難なところには、部分的な機械の空運転モードを組み合わせてラインの隅々をモニターする。すべての検査結果は1台のコンピュータに集約し、画像データはAIで解析する。
ラインの搬送コンベア上と機械の下の残留物の確認は、自動チェックによりわずか1分程度で完了する。これにより、ラインクリアランスにかかるトータルの時間は約10分に短縮された。
「従来と比べて、より早く、より安全で、より確実に改善されました。そして効率化できた分、スタッフは新たな改善活動や教育に時間を使うことができるようになりました」
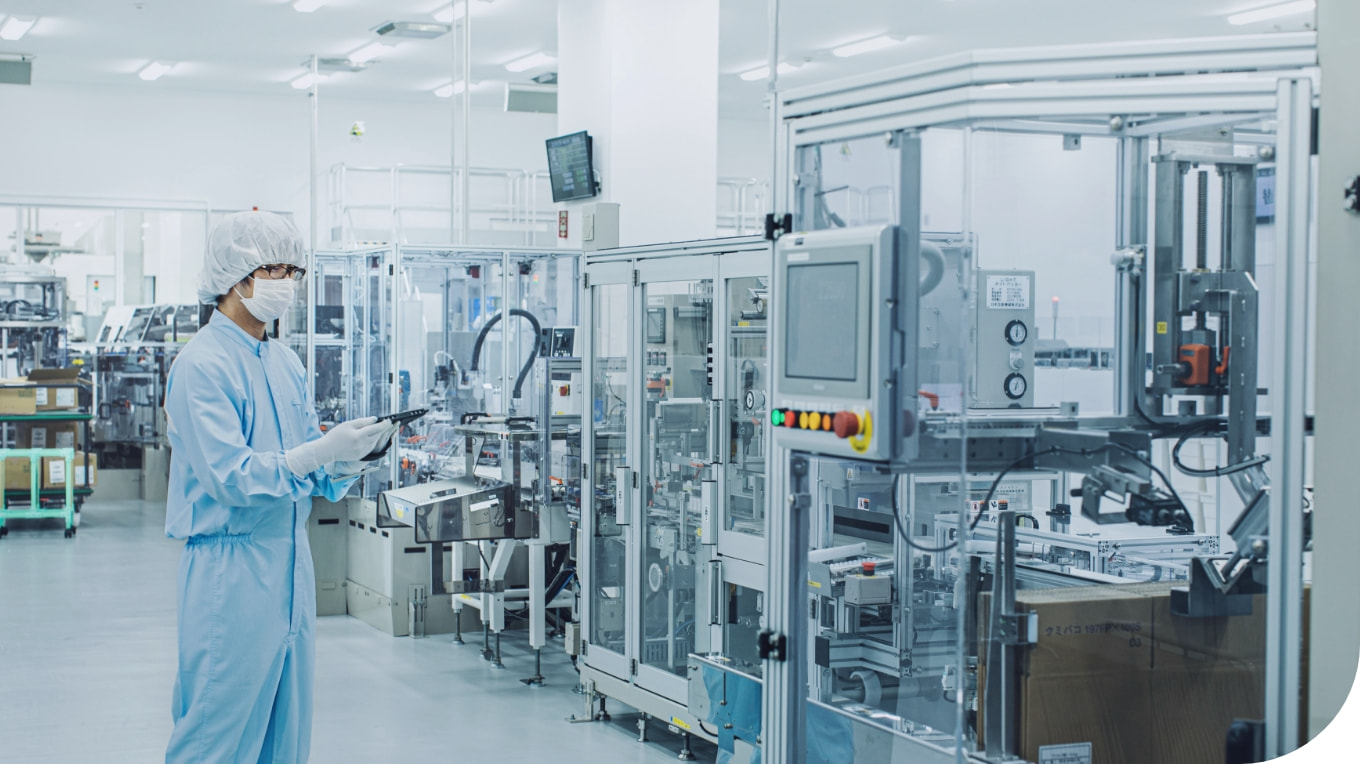
※2 添付文書:患者さんの安全を確保し医薬品を適正に使用してもらうために、医療従事者に対して必要な情報を提供する目的で製薬会社が作成する書面
困難を極めたALCの開発
ALCの開発・導入を決めたのは、2017年に遡る。社内のブレーンストーミングによってアイデアが生まれた。当時、製剤技術部に所属し、包装施設立ち上げのプロジェクトリーダーを務めた近藤は、その時の様子をこう振り返る。
「20年、30年先の未来を見据えた工場にするために何が必要かを考えてほしいという会社からのミッションを受け、現場のオペレーターを含めて意見を出し合いました。そのなかで出てきたのがALCです」
和田もそのブレーンストーミングに参加していたひとりだ。
「私もALCはすごく良いアイデアだと思い、賛成に手を挙げたのを覚えています。でも、当時はまさか実現できるとは思っていませんでした。きっと夢で終わるだろうなと……」
これまで、どの製薬会社も実現していないということは、世の中に参考にするものがないということでもある。ゼロベースからの開発は困難を極めた。
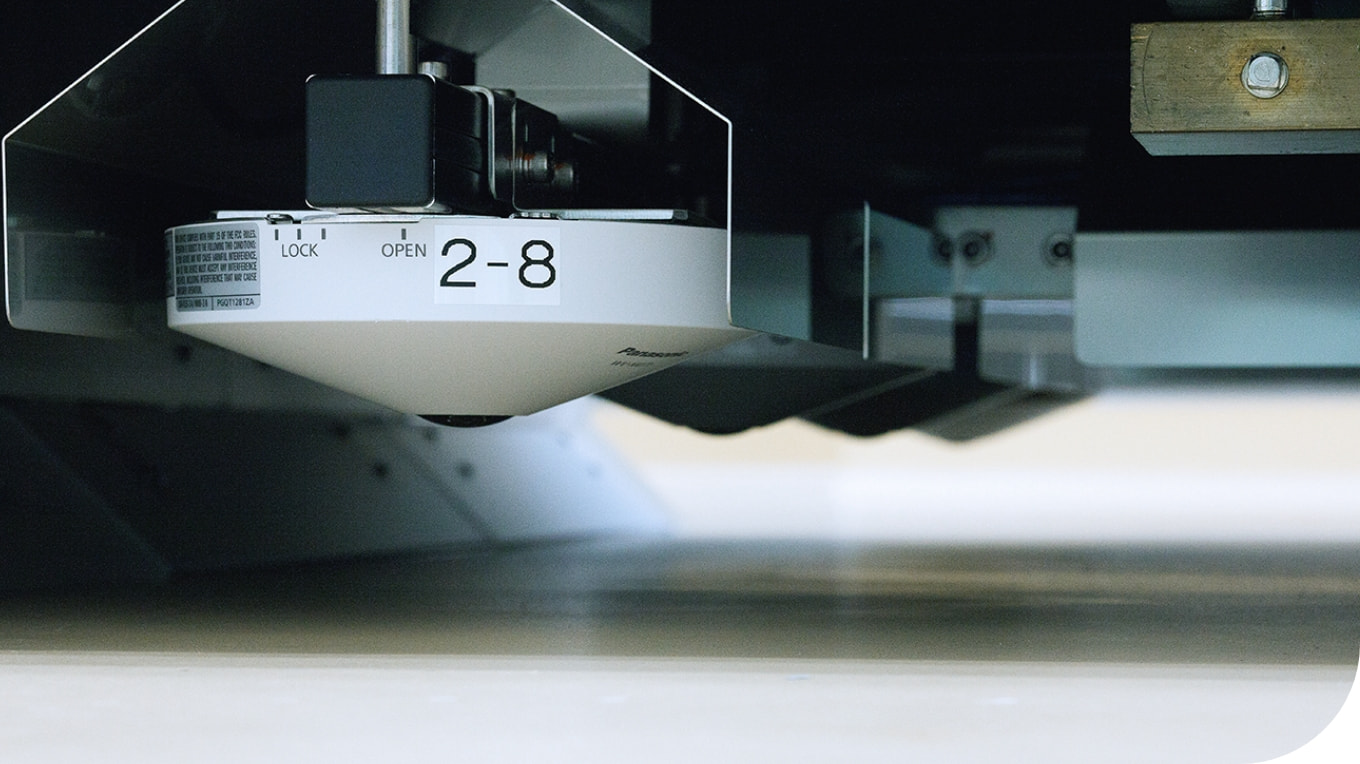
「360°カメラを使って画像を撮影し、AIに解析させようという考えはあったのですが、そもそもカメラといっても数え切れないほど種類があります。さらに、カメラの台数が多ければシステムもそれに応じて複雑になるので、コンピュータの処理時間がかかり、結果的にALCを完了させるまでの時間が長くなります。そのため、システムをできるだけシンプルにしつつ、残留物の見逃しがないよう、どんなカメラをどこに何台配置するかを検討するのに、大変苦労しました」
カメラの位置を決めたり、解析ソフトを開発したりするには、実際の機械を使ってトライ&エラーを繰り返す必要があるが、製造エリア内に持ち込むことは異種混入のリスクにつながる。
そこで、別の部屋に実際の設備を模擬したテスト用の環境を作った。
このようにさまざまなハードルを乗り越えるために試行錯誤を繰り返し、約2年をかけてALCを含むオートメーション包装施設が完成した。
「あまりのプレッシャーに何度も心が折れそうになりました」と、近藤は振り返る。それでも実用化できたのは、製薬業界で初の試みにチャレンジしているという自負と、揺るぎない想いからだった。
「最新技術を積極的に導入することでヒューマンエラーが削減されれば、工程が安定化し、製品を計画通り出荷することができます。この薬を待っている患者さんや、医療現場に届けたい。その想いがあったからこそ実現できました。どんな困難な場面でも、プロジェクトのメンバーが付いてきてくれたこと、そして、タケダのグローバルエンジニアリングチームがサポートしてくれたことも強力な後押しになりました」
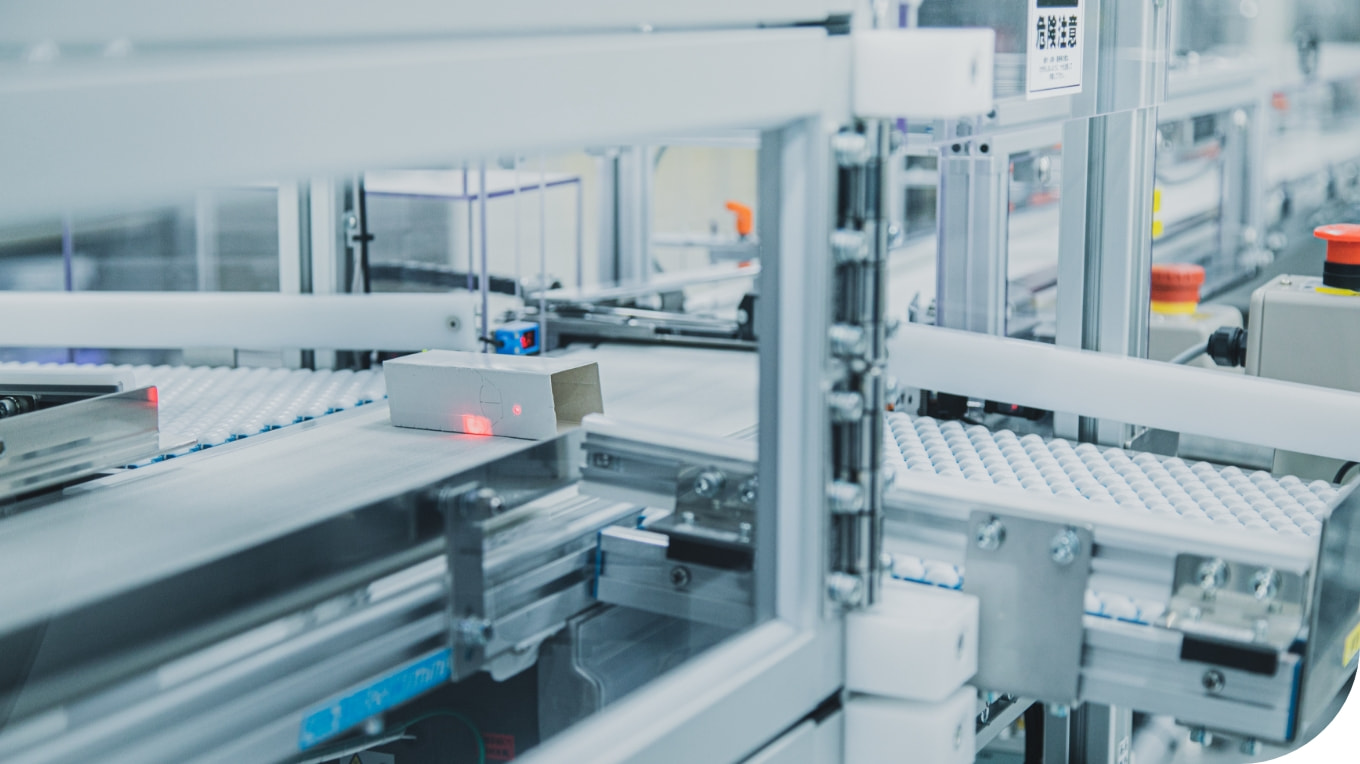
世界が認めた光工場の技術
光工場の固形製剤包装施設は、2021年、国際製薬技術協会(ISPE)が選ぶファシリティー・オブ・ザ・イヤー・アワード(年間優秀施設賞)の「プロセスインテリジェンス&イノベーション」部門での受賞を果たした。
これは、革新的なテクノロジーを活用して製品の品質向上や製造コストを削減した、最先端のプロジェクトを表彰する賞である。
「世界のトップ製薬企業がエントリーする権威ある賞なので、まさか受賞できるとは思っておらず、本当に驚きました。なかなか信じられなかったのですが、アメリカから届いたトロフィーを見たときに、しみじみと実感が湧いてきました」と、近藤はその時の喜びを語る。
「医薬品包装における新たな業界スタンダードとなるべく、患者さんを中心に考え、努力してきたことが革新的技術だと認められたのは、素直にうれしかったです」
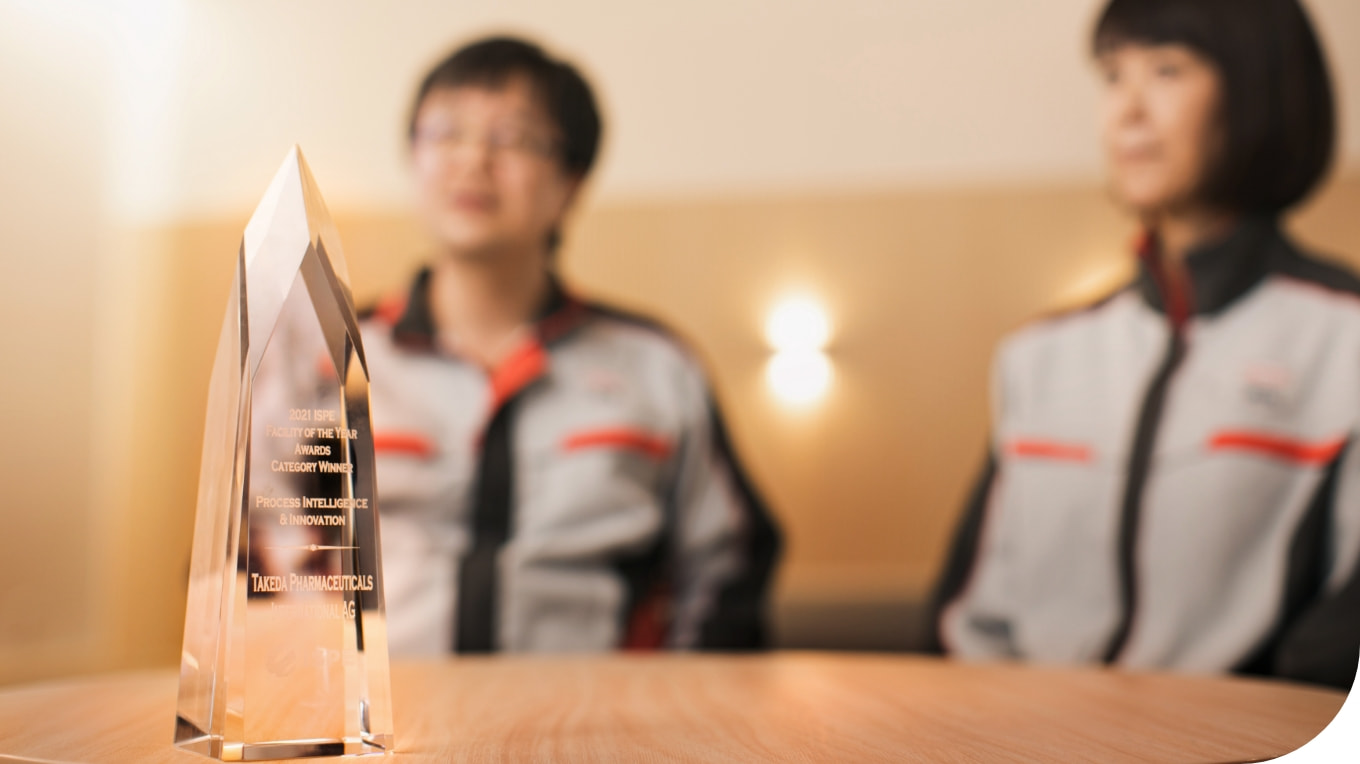
現場で働く人とデジタルを
組み合わせて
製薬業界を牽引
今回の成功の背景を、近藤はこう分析する。
「ニーズがないものを、技術ファーストで無理やり現場に入れても成功しません。現場が望んでいるものは何なのか、まずは現場ありきで考え、次にそれに結び付く技術を考えるというアプローチが大切だと実感しました」
最新の技術を活用し、医薬品の品質を維持しながら効率良く生産しお届けする方法を、現場の人と共に考える。その想いは現場のマネジャーである和田も同じだ。
「人の命に関わる医薬品の製造には、大きな“責任”が伴います。リスクを徹底的に回避する自動化システムと併せて、私たちが大切にしているのは“Quality Culture”です。Quality Culture とは『物事をシンプルにすること』、『正しい行いに誇りをもつこと』、『スピークアップできる文化を創ること』、そして『品質への取り組みを行動で示すこと』です。この4つをチームメンバーに浸透させ、文化として根付かせています」
近藤も、技術革新には現場の声を聴くことが大切だと考えている。
「日々どれだけ緻密にメンテナンスをしていても、機械は最初に導入した状態から少しずつ変わっていきます。すると、毎日同じ製品を作っていても、目には見えない誤差が生じます。そのような微妙な変化に気づけるのは現場のオペレーターですが、彼らの声をいかに吸い上げられるか、そこにヒントが眠っていると思います」
近藤が考えている次の技術革新は、データに基づいて製造を調整する、データ・ドリブン・マニュファクチャリングだ。
「製造ラインには、データを集めるためにさまざまな機器を取り付けています。最近では、リアルタイムで計測したデータをサーバにアップし、オペレーションルームでグラフ化して表示させ、日々の朝礼で活用する取り組みを始めました。今後は更にこのデータをAIで解析することで、設備のトラブルを未然に予知したり、防止したりすることができないかと、データ分析の専門家であるデータサイエンティストと協力しながら、新たな試みを始めています」
ALC開発・導入で得られたノウハウは、世界中にあるタケダの製造拠点はもちろん、社外にも共有していく予定だ。
最先端の技術として認められてもこれで満足することはない。「まだまだ先がある」と、近藤は言う。
「私たちは品質、コスト、供給、すべての面で、世界最高レベルの医薬品包装施設になることを目指しています。光工場が業界全体をグローバルに牽引する存在となるように、ますます気を引き締めていきます」
タケダの医薬品包装技術をさらなる高みに引き上げるために、そして、患者さんに品質の高い医薬品をより早く届けるために、これからも光工場は進化を続ける。
PROFILE
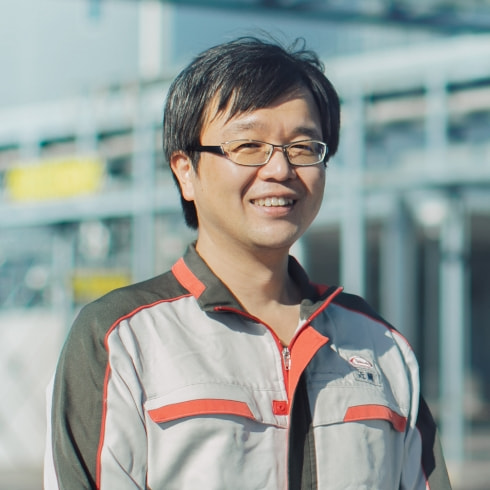
光工場
インスペクション&パッケージング部
近藤 昌博
高度な自動化を実現する光工場にて、GMPを順守した医薬品包装と検査の製造管理責任者として組織を統括する。デジタルの活用推進プロジェクトをきっかけに、自動ラインクリアランスの開発と導入を指揮した。
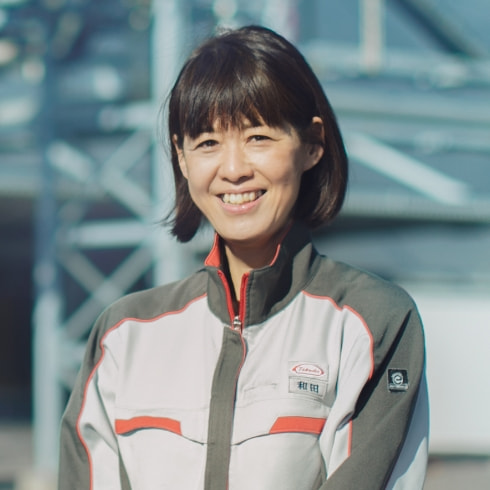
光工場
インスペクション&パッケージング部
和田 佳子
医薬品のPTP包装を担当するチームを束ねる。GMP順守のもと、手順に即した作業と記録を徹底し、リスクの早期発見と早期対応を可能にする仕組み、高品質にこだわる文化や環境づくりにも取り組む。
※所属は撮影当時のものです